Карбон. Свойства и применение. Плюсы и минусы. Особенности
Карбон – это полимерный очень прочный композитный материал, состоящий из эпоксидной или другой смолы, и армированный углеродными волокнами. Также его называют углепластиком или карбонопластиком. Главная особенность композита в высокой прочности при небольшой толщине и легкости.
Углепластик является сложным композитным материалом, при изготовлении которого требуется прикладывание ручного труда. В связи с этим цена на него примерно в 20 раз выше, чем на качественную сталь европейского производства.
Вся сложность процесса его изготовления заключается в применяемом армирующем компоненте – углеволокне. Оно представляет собой тончайшие нити, практически на 99% состоящие из атомов углерода. Их получают путем сложного сжигания органических волокон с поэтапным поднятием температуры. В результате от них остается только углерод, который меняет свою структуру, приближаясь к графиту.
Нити углеволокна имеют толщину всего 0,005-0,10 мм. Они тоньше, чем человеческий волос. Каждую из них по отдельности очень легко сломать, но трудно разорвать. Из волокон сплетают полотна, которые и применяются для изготовления карбона.
Углеволокно работает как армирующий компонент карбона. Из него изготавливаются различные тканые и нетканые материалы. Такие холсты пропитываются полимерными смолами, чаще всего эпоксидными. Слои углеволокна наклеиваются друг на друга. В итоге по застыванию смолы, композитный материал приобретает повышенную прочность, гибкость и стойкость к излому. Практически нет аналогичных композитов, которые можно сопоставить по этим качествам с карбоном. Ему уступает стеклопластик и прочие аналоги.
Сфера использованияИзначально карбон был предназначен исключительно для изготовления облегченных деталей спортивных гоночных автомобилей, а также космических аппаратов. Позже себестоимость его производства снизилась достаточно, чтобы применять его и для других целей.
Сейчас из него делают:
- Детали авиационной техники.
- Удилища для рыбалки.
- Спортивный инвентарь, такой как хоккейные клюшки, шлемы и т.д.
Ежегодно производится практически 40-45 тыс. тонн карбона. Из них львиная доля в 41% потребляется авиацией, а также космической и военной промышленностью. Из него делают легкую прочную экипировку, детали для оружия, типа прикладов, рукояток и т.д. Как не удивительно, но 17% композита расходуется на получение спортивного инвентаря, а для строительной сферы только 12%. Примерно 5% уходит на автомобилестроение, и 2-3% на изготовление бланков удилищ.
Технологии изготовления карбоновых изделийЧтобы получить карбон, необходимо пропитывать слои ткани из углеволокна смолой, и склеивать их между собой. Это можно делать тремя основными способами:
- Приклеивая.
- Спрессовывая.
- Наматывая.
Чаще всего пользуются самым простым способом, заключающимся в наклейке холста на поверхность. Затем он пропитывается сверху смолой, и на него вклеивается следующий слой. Таким образом, набирается нужное количество слоев, чтобы достигнуть требуемого уровня прочности материала и его толщины. Этим методом пользуются в домашних условиях особенно часто, так как для него не требуется особый инструмент и различные приспособления. Смола наносится на углеволокно кистью, тщательно пропитывая ее. Стоит отметить сложность и кропотливость процесса. Зачастую чтобы получить слой карбона толщиной всего в 1 мм, нужно клеить холст в 4 слоя.
Изделия из углекарбона на производствах зачастую получают методом прессования. Это позволяет добиться лучшего удаления воздуха между слоями. В итоге готовое изделие получается более прочным и надежным. Преимущество метода еще и в том, что спрессованная заготовка может разогреваться, для ускоренной полимеризации смолы. При этом благодаря прессу композит будет все время держать правильную форму, пока не затвердеет. Эта технология дает более высокую производительность.
Также изделия их карбона цилиндрической формы можно получать методом намотки. Эта технология подходит как для заводского, так и домашнего производства. Именно этим методом делаются удилища для рыбалки, спиннинги, рамы велосипедов и т.д. Холст углеволокна наматывается на трубку, и пропитывается смолой. В итоге достаточно быстро набирается большое количество слоев, которые в итоге дают высокую прочность изделию. Трубка же, на которую все изначально наматывалось, вынимается. Чтобы она не приклеилась, ее предварительно смазывают специальным разделительным составом. Тогда адгезии смолы к ней не происходит.
Карбон это очень востребованный материал, что обусловлено его положительными качествами:
- Легкость.
- Термическая устойчивость.
- Стойкость к коррозии.
- Упругость.
Изделия из карбона нельзя назвать легкими, но если сравнивать его с металлами такого же объема, то он неоспоримо легче. К примеру, сталь тяжелее на 40%, а алюминий на 20%. Но нужно сразу же отметить прочность карбона. Из него можно делать тонкие изделия и использовать в таких условиях, в которых бы не справились аналоги из стали такой же толщины.
Материал обладает очень высокой термической стойкостью. Отдельные образцы карбона нормально переносят нагрев до температур до +2000С. Само углеволокно легко переносит такие условия, но только в бескислородной среде. Но так как оно находится в толще застывшей смолы, то не контактирует с воздухом. В конечном итоге температурная стойкость карбона продиктована больше свойствами смолы, из которой он изготавливается.
Материал не ржавеет и не подвергается другим видам коррозии. Это делает его альтернативным решением для применения вместо стальных изделий в сложных условиях. Он нормально переносит воздействие ультрафиолета, так что может эксплуатироваться практически где угодно.
Карбон является очень упругим материалом, который сложно сломать. За счет этого он так ценится при изготовлении различного спортивного инвентаря. Не последнюю роль в этом играет и его сравнительная легкость, и то что изделия из него за счет прочности можно делать меньшего сечения, чем из дерева, металла или другого пластика. Высокий предел упругости подтверждают хоккейные клюшки, теннисные ракетки и луки, которые делают из карбона.
Качество карбона во многом зависит от того, каким образом был сделан холст из углеволокна, и во сколько слоев уложен. Дело в том, что ориентируя направление волокон в слоях можно добиваться большей стойкости готового изделия на воздействие под определенным углом. Так можно корректировать упругость и стойкость на излом.
Недостатки карбонаКарбон является весьма ценным материалом, поэтому изделия из него очень качественные. Они более удобные в эксплуатации, однако, все же не идеальные. Проблема в том, что материал боится ударной нагрузки. От этого на нем появляются трещины и сколы. Зачастую они незаметны, но их появление существенно уменьшает прочностные характеристики композита. Зачастую достаточно деформации карбона даже на 0,5%, чтобы вызвать его структурные нарушения. Однако это не означает, что в итоге изделие из него покроется видимыми трещинами и сколами, а потом сразу же сломается. В композите просто появляются микротрещины, но он все равно остается достаточно прочным, чтобы справлялся с теми задачами, которые перед ним стоят.
Качество композита может сильно отличаться, так как напрямую зависит в первую очередь именно от применяемого углеволокна. В процессе его получения нарушить технологию нельзя, в частности не допускается делать даже небольшое отклонение в температурном режиме или продолжительности воздействия на него, так как прочность готового армирующего компонента снижается. В итоге карбон из него также будет менее стойким на излом. Таким образом, стоимость на композитные изделия из карбона разных производителей существенно отличается.
Материал все же не разлетается на осколки при ударах, так как его части удерживаются между собой слоями из углеволокна. Проблема композита в том, что в нем сложно найти баланс между эластичностью и упругостью. Если он отлично переносит воздействие на разрыв, то зачастую достаточно легко ломается при прикладывании усилия на излом. В связи с этим существует большой процент изделий из карбона, которые в результате нарушения расчетов при изготовлении служат не так долго как заявлено для этого композита. Это яркое подтверждение того, почему одни предметы из карбона стоят в разы дороже, чем на первый взгляд такие же других производителей.
Высокая стоимость карбона, не позволяет его использовать в направлениях, где это экономически нецелесообразно. Композит имеет очень привлекательный внешний вид, поэтому не нуждается в декорировании. По причине его внешних качеств, производятся различные полимерные пленки, имитирующие карбон. При этом они сами по себе им не являются. Это просто декоративные изделия, похожие на него внешне за счет характерного рисунка.
Никакого увеличения прочности поклейка такой пленки не дает, так как она далека от карбона. Она просто обеспечивает декоративный эффект, а также дает некоторую защиту от влаги. По сути это просто слой декорации, ничего более. Так что не стоит путать композит и карбоновую пленку.
Похожие темы:
- Паронит. Свойства и особенности. Производство и применение
- Арамидный материал. Виды и применение. Свойства и особенности
- Асботекстолит. Виды и особенности. Свойства и применение. Работа
- Гетинакс. Виды и применение. Производство и особенности работы
- Текстолит. Форма производства и марки. Плюсы и минусы. Особенности
- Стеклотекстолит. Состав и применение. Свойства и особенности
- Армирующая сетка. Виды и применение. Материал и особенности
- Стеклоткань. Свойства и применение. Плюсы и минусы. Особенности
- Стекломат. Назначение и применение. Плюсы и особенности
- Латекс. Виды и свойства. Применение и особенности
Почему карбон не используется в массовом автопроме — Автомобили
Карбон – народное название, транслитерированное с английского слова carbon – уголь, которое в свою очередь было заимствовано еще из латыни. Углепластик представляет собой полимерный композиционный материал, состоящий из нитей углеродного волокна, переплетенных под определенным углом — как шерсть в свитере. Только очень прочный, с высокой степенью натяжения, низким весом и низким температурным расширением. Из-за его дороговизны композит может применяться как усиливающее дополнение, например, к стали — тогда материал получит приписку «усиленно углепластиком», CFRP.
Зона применения
Свою блистательную карьеру карбон начал с ракетных двигателей, а сегодня применяется в самых различных сферах — от производства удочек до самолетостроения. И в автопромышленности — не в последнюю очередь, прежде всего, в структуре кузова, а также элементах отделки экстерьера и интерьера.
Углепластик хорош тем, что обладает высокой прочностью, жесткостью и малой массой — он прочнее алюминия и легче стали, оказываясь более эффективным материалом. У кузова, изготовленного с применением композита, больше жесткость на кручение, что играет на руку безопасности автомобиля, и выше стойкость к коррозии. Даже применение части карбоновых деталей, даже только в отделке интерьера, снижает массу автомобиля, а значит, повышает топливную экономичность и динамические характеристики. При массовом применении повысилась бы и общая безопасность на дорогах при авариях, а также безопасность пешеходов.
Да и просто карбон считается красивым и стильным материалом — ведь спросом пользуется даже имитация «под карбон», которую с удовольствием используют в деталях и интерьере недешевых машин. Что уж говорить о пленке «под карбон», которая не добавляет кузову ни прочности, ни легковесности.
Однако из-за своей дороговизны углепластик далек от рынка массовых автомобилей и используется только в эксклюзивных дорогостоящих моделях, а также автоспорте. Но почему этот материал в прямом смысле «на вес золота»?
Дорогое производство
Окончательный ценник автомобиля в автосалоне складывается из сотни факторов: необходимость окупить затраты на создание идеи и разработку проекта, зарплаты дизайнеров и маркетологов, стоимость рекламы и имидж бренда. И мы можем только догадываться, насколько отличается себестоимость автомобиля от его покупательской цены.
Затраты на производство кузова с применением углепластика, его обработка и сборка мало чем отличаются от той же стали. Однако причина дороговизны композитной автомобильной детали объективна — дорог сам материал. Стоимость сырья составляет 20 долларов за килограмм, в то время как килограмм стали обойдется менее чем в один доллар.
Во-первых, из-за высокого спроса (например, из-за широкого применения в самолетостроении) на рынке наблюдается дефицит волокна, что также играет на его подорожание.
Во-вторых, сам процесс производства углеволокна очень трудоемкий и дорогостоящий. Итак, начинается все еще с нитей, из которых «вяжется» карбоновая пластина. Углеродные волокна получают за счет термической обработки химических и природных органических волокон, при которой в материале волокна остаются главным образом атомы углерода. Сначала происходит окисление исходного волокна – на воздухе при температуре 250 градусов Цельсия в течение 24 часов, потом стадия карбонизации — нагрев волокна в среде азота или аргона при температуре от 800 до 1500 градусов Цельсия, а затем графитизация в инертной среде при температуре 1600-3000 градусов. В результате количество углерода в волокне доводится до 99%.
И на выходе одно только стартовое сырье становится в два раза дороже, чем исходный материал, так как половина элементов просто сгорает. Не считая расходов на специализированное оборудование и затрачиваемую энергию — представьте, сколько это стоит при обработке в перечисленных выше условиях и температурах, да и сами автоклавы (оборудование) значительно дороже. Более того, нужно избавиться от исключенных элементов, а утилизация этих «отходов производства», не вредящая окружающей среде, еще один важный пункт в счете расходов.
И это мы только сделали нити, а ведь из них еще надо «сплести полотно», которое и будет обладать той удивительной прочностью. И прежде всего, придется убедиться, что все нити одинаковы и равномерно растягиваются, иначе в полотне какие-то из них будут более уязвимы, а следовательно, сломаются. Так что необходимы сложные и дорогостоящие меры контроля качества изделий — в случае ошибки при производстве материал окажется хрупким, а не суперпрочным.
Затем нити работают с термоактивными смолами, которые их «склеивают», в результате и получается композит. Эти смолы также дороже обычных. А ведь композиту еще нужно придать форму, что занимает около часа — очень долго, если сравнивать с тем, как быстро штампуются кузовные панели из стали. Деталь из углепластика производится двумя способами. При прессовании углеткань выстилается в форму, смазанную антиадгезивом (например, мылом), пропитывается смолой, излишки смолы удаляются в ваккуме или под давлением, смола полимеризуется. Второй вариант — контактное формование: берется исходная деталь (например, металлический бампер), смазывается разделительным слоем, сверху напыляется монтажная пена. После затвердевания слепок смазывают разделительным слоем и выкладывают пропитанную углеткань, которая прокатывается, полимеризуется и затем снимается.
И наконец карбон, несмотря на свою прочность, уязвим для точечных ударов, а треснувший углепластик плохо пригоден к ремонту. Невидимые глазу внутренние трещины и расслоения приводят к снижению плотности. Скорее всего, поврежденную композитную деталь автомобиля придется заменять.
Вот что рассказал порталу «АвтоВзгляд» директор по послепродажному обслуживанию «Ауди Центр Восток» Алексей Кирдяшов:
— Высокая стоимость углепластика объясняется в первую очередь тем, что для изготовления карбона требуются высококачественные дорогостоящие компоненты и используется сложный процесс производства. На цену материала также влияют его уникальные характеристики — прочность и легкость. Это естественно, что за такое «ноу-хау» и эксклюзивные свойства продукта производители делают наценку, объясняя это тем, что карбон — будущее в автомобилестроении, авиастроении, изготовлении электроники, строительстве и многом другом. Продукт пользуется спросом, но еще не используется массово из-за своей стоимости…
Путь к удешевлению
Но коль дорого стоит производство, а не сам «алмаз», то его можно удешевить, упростив и удешевив технологию получения углеволокна. И, судя по последним заявлениям, производители композитов уже близки к этому. Ради совершенствования технологий производства карбона создан специальный немецкий проект MAI Carbon, на который работает более 70 компаний, институтов и лабораторий, в том числе Audi и BMW. И по словам его руководителя Клауса Дрекслера, затраты на производство углеволокна могут быть снижены на 90%. В результате композит может стать значительно дешевле, а значит, доступным для массового автомобильного производства. А при увеличении объемов производства кузова из углепластика станут стоить столько же, сколько стальные, и появятся у дешевых автомобилей.
По словам Дрекслера, для удешевления и ускорения производства нужно сделать процесс более автоматизированным. Подробностей участники проекта пока не раскрывают, однако в качестве реального примера можно вспомнить литиевые батареи, которые в последние годы удается делать все более доступными. Пассажирская клетка электрокара BMW i3 выполнена из композита, а ведь это уже массовая модель.
Например, технология струйного переноса сухой смолы, разработанная и запатентованная австралийской компанией Quickstep на средства правительства, уже позволяет автоматизировать изготовление кузовных панелей. Робот распыляет смолу особого состава в сухом виде, что позволяет избавиться от дорогостоящей подготовки жидкой смолы. Анализируется применение в качестве карбонового сырья лигнина, который получают из древесины и который по прочности на сжатие соответствует бетону, или подогрев при помощи плазмы. Ищут способы заставить углепластик работать с термопластиковыми смолами, что может удешевить производство на 60-70% и упростить устранение ошибок.
Похоже, революция на пороге.
Материалы из углеродного волокна | Ткань, рукава, ленты и жгут
Углеродное волокно — это прочный, легкий и жесткий материал, изготовленный из тонких и прочных кристаллических нитей углерода. Его изготавливают путем нагревания и растяжения углеродных нитей до тех пор, пока они не станут длинными тонкими волокнами, которые затем сплетаются или сплетаются вместе, образуя ткань. Материалы из углеродного волокна известны своей высокой прочностью и малым весом, и они часто используются в различных областях, где эти свойства важны, например, в аэрокосмической, морской и автомобильной промышленности, а также в спортивных товарах и других потребительских товарах. продукты.
Углеродное волокно можно использовать во многих формах, включая тканые ткани, оплетки и однонаправленные листы. Их обычно комбинируют со смолами или металлами для создания композитных материалов с еще более желательными свойствами. Изделия из углеродного волокна часто используются вместо стали или других традиционных материалов для снижения веса и улучшения характеристик конструкции или изделия.
Fiber Glast Developments предлагает широкий выбор армирующих материалов из углеродного волокна, включая ткань, рукава, жгут и ленту. Мы прилагаем все усилия, чтобы гарантировать, что все продукты, с которыми мы работаем, имеют первоклассное качество и изготовлены в соответствии с самыми высокими стандартами для максимальной прочности и идеальной косметики. Независимо от того, какой продукт из углеродного волокна вы выберете, его всегда следует использовать с соответствующей системой смол. Чтобы максимизировать прочностные характеристики вашей детали из углеродного волокна, мы предлагаем вам использовать эпоксидную смолу, такую как Fibre Glast System 2000. В сочетании они будут производить высококачественные, жесткие, усиленные детали.
Щелкните изображение углеродного волокна ниже, чтобы получить дополнительную информацию и просмотреть цены.
1 2 3 4
Материалы и композиты из углеродного волокна являются предпочтительным выбором во многих отраслях промышленности из-за их высокой прочности на растяжение, жесткости, отношения прочности к весу, термостойкости, химической стойкости и в целом высококачественной конструкции. При всех своих преимуществах изделия из углеродного волокна стоят недорого по сравнению с аналогичными волокнами.
Использование материалов из углеродного волокна и отрасли промышленности
Изделия из углеродного волокна обычно используются во многих отраслях промышленности, где требуется материал, обеспечивающий высокое качество и прочность, присущие материалам из углеродного волокна.
- Армия: Армия — это то место, где сила и высокое качество являются абсолютной необходимостью. Некоторые из его применений включают баллистическую защиту из кевлара, карбоновые конструкции жесткости, а также тактические цевья и прицелы.
- Аэрокосмическая промышленность: Уменьшение прочности и веса высоко ценится в аэрокосмической промышленности. Некоторые из его применений включают лопасти вентилятора турбины, рулевые тяги и компрессионные стойки.
- Промышленность: Промышленное применение требует надежности и прочности материалов из углеродного волокна. Некоторые из применений включают роботизированные руки, оборудование для защиты от ударов и осветительные опоры.
- Спорт: легкий вес означает скорость, поэтому высококачественные велосипедные рамы изготавливаются из углеродного волокна. Кроме того, мотогонщики нуждаются в защите и часто выбирают гоночные перчатки из углеродного волокна.
Изделия из углеродного волокна
Волокно Glast Developments предлагает высококачественные изделия из углеродного волокна для различных областей применения.
- Ткань: Ткани из углеродного волокна бывают саржевого, полотняного, атласного и однонаправленного переплетения. Все ткани обладают той же прочностью, жесткостью и высококачественной конструкцией, что и все наши изделия из углеродного волокна. Втулки
- : Втулки из углеродного волокна легко надеваются на цилиндры, образуя прямую или коническую трубку. Они соответствуют форме продукта и улучшают характеристики при минимальном весе. Ленты
- : Хотя на них нет клея, эти ленты из углеродного волокна называются лентами из-за их формы. Они используются для выборочного армирования компонентов из углеродного волокна.
- Пакля: жгут из углеродного волокна используется для плетения тканей из углеродного волокна. Его также можно использовать для изготовления намотанных деталей, пултрузии, рубленых углеродных волокон или в качестве местного армирования.
- Вуаль: Хотя графитовые вуали не предназначены для использования в строительстве, они используются в качестве коррозионно-стойких барьеров. Они также могут уменьшить накопление статического электричества в приложениях, связанных со взрывоопасными жидкостями или газами.
Компания Fiber Glast Developments имеет более чем 65-летний опыт дистрибуции стекловолокна и композитов. Мы сертифицированы по стандарту ISO и гарантируем, что характеристики нашей продукции соответствуют высочайшему качеству. Наша система экспресс-заказов гарантирует доставку в тот же день, если вы заказываете до 14:30 по восточному поясному времени. Все заказы подтверждаются нашей первой гарантией качества, которая гарантирует, что наша продукция производится в соответствии с самыми высокими стандартами.
Узнайте больше об углеродном волокне и других композитных материалах от наших экспертов из Fiber Glast. У нас есть бесплатный Учебный центр с официальными документами, видео, диаграммами, фотогалереями и многим другим. Начните работу с наших бесплатных технических документов, в том числе «Об армировании» и «О препрегах».
Подробнее/Меньше
Этот веб-сайт использует файлы cookie, чтобы обеспечить вам максимальное удобство. Узнать больше
Принимать
Что такое углеродное волокно? | DragonPlate
Содержание
- Что такое углеродное волокно?
- Как выглядит углеродное волокно?
- Создание композитов из углеродного волокна
- Свойства углеродного волокна
- Сравнение углеродного волокна с алюминием и сталью
- Высокомодульное углеродное волокно
- Потенциальные характеристики композитов из углеродного волокна
- Что такое сэндвич-структура из углеродного волокна?
- Плюсы и минусы композитов из углеродного волокна
- Углеродное волокно в сравнении с металлами
- Производство углеродного волокна для пользовательских применений
Углеродное волокно представляет собой материал, состоящий из тонких, прочных кристаллических нитей углерода, в основном атомов углерода, связанных друг с другом в длинные цепочки. Волокна чрезвычайно жесткие, прочные и легкие и используются во многих процессах для создания превосходных конструкционных материалов. Углеродное волокно обладает рядом преимуществ, в том числе:
- Высокая жесткость и соотношение жесткости к весу
- Высокая прочность на растяжение и соотношение прочности к весу
- Высокотемпературная толерантность со специальными смолами
- Низкое тепловое расширение
- Высокая химическая стойкость
Что выглядит углеродолоколодос.
Углеродное волокно изготавливается из черных нитей или нитей, называемых «жгутами», и поставляется в различных форматах, включая катушки жгута, однонаправленные форматы, переплетения, оплетки и другие, которые используются для создания деталей из углеродного волокна.
Внутри каждого из этих форматов есть подкатегории дальнейшего уточнения. Например, различное переплетение углеродного волокна может привести к различным свойствам композитной детали.
Создание композитных материалов из углеродного волокна
Для создания композитной детали углеродные волокна, жесткие при растяжении и сжатии, должны поддерживаться в стабильной матрице для сохранения формы детали. Эпоксидная смола является отличным пластиком с хорошими физическими свойствами и часто используется для этой матрицы, а углеродные волокна обеспечивают прочность.
Поскольку и эпоксидная смола, и углеродное волокно имеют низкую плотность, можно создать легкую, но очень прочную деталь. При изготовлении композитной детали можно использовать множество различных процессов, включая мокрую укладку, вакуумную упаковку, перенос смолы, согласованную оснастку, литье под давлением, пултрузию и многие другие методы. Кроме того, выбор смолы позволяет подобрать определенные свойства, такие как устойчивость к повышенным температурам или химическим веществам.
Углеродные волокна, армирующие стабильную матрицу из эпоксидной смолы
Свойства углеродного волокна
Углеродное волокно чрезвычайно жесткое, прочное и легкое. В машиностроении обычно сравнивают свойства материалов с точки зрения их отношения прочности к весу и отношения жесткости к весу, особенно при проектировании конструкций, где дополнительный вес может привести к увеличению стоимости жизненного цикла или неудовлетворительным характеристикам.
Модуль упругости и предел прочности углеродного волокна
Жесткость материала измеряется его модулем упругости. Это очень похоже на Spring Rate, метрику, используемую для описания жесткости пружин. Он рассчитывается путем деления изменения напряжения на изменение деформации. Модуль углеродного волокна обычно составляет 33 миллифунта на квадратный дюйм (228 ГПа), а его предел прочности при растяжении обычно составляет 500 тысяч фунтов на квадратный дюйм (3,5 ГПа).
Механические свойства деталей из углеродного волокна
Жесткость и прочность по любой конкретной оси в детали из углеродного волокна зависят не только от механических свойств волокна и смолы, но также от размещения и ориентации волокна, а также от соотношения волокно/смола (обычно примерное соотношение 50/50). Типичное значение жесткости композитной пластины из углеродного волокна составляет 10 мфунтов на квадратный дюйм, а ее прочность — 90 тысяч фунтов на квадратный дюйм.
Отношение жесткости к весу
Ламинат полотняного переплетения, армированный углеродным волокном, имеет модуль упругости приблизительно 8 msi и объемную плотность приблизительно 0,05 фунта/дюйм 3 . Отношение жесткости к весу для этого материала составляет 160 x 10 6 . Для сравнения, плотность алюминия составляет 0,10 фунта/дюйм 3 , что дает отношение жесткости к весу 100 x 10 6 . Плотность стали 4130 составляет 0,30 фунта/дюйм 3 , что дает отношение жесткости к весу 100 x 10 6 .
См. таблицу ниже
Материал | Модуль упругости | Объемная плотность | Жесткость-масса |
Композитный материал из углеродного волокна с полотняным переплетением | 8 msi | 0,05 фунта/дюйм 3 901 37 | 160 x 106 6 |
6061-T6 Алюминий | 10 msi | 0,10 фунта/дюйм 3 | 100 x 10 6 |
Сталь | 90 175 30 msi0,30 фунта/дюйм 3 | 100 x 10 6 |
Следовательно, даже базовая панель из углеродного волокна с полотняным переплетением имеет отношение жесткости к весу на 60% больше, чем алюминиевая или стальная.
Сравнение углеродного волокна с алюминием и сталью
Сравните вышеприведенное с алюминием 2024-T3, который имеет модуль 10 мфунтов на квадратный дюйм и предел прочности при растяжении 65 тысяч фунтов на квадратный дюйм, и сталь 4130, которая имеет модуль 30 мфунтов на квадратный дюйм и предел прочности при растяжении прочность 125 тыс.фунтов/кв.дюйм.
Предел текучести углеродного волокна по сравнению со сталью
Сталь будет постоянно деформироваться при уровне напряжения ниже предела прочности при растяжении. Уровень напряжения, при котором это происходит, называется пределом текучести. Углеродное волокно, с другой стороны, не будет постоянно деформироваться ниже своего предела прочности на растяжение, поэтому оно фактически не имеет предела текучести.
Высокомодульное углеродное волокно
Углеродное волокно более высокой жесткости доступно через специальные процессы термообработки. Использование препрега, а также препрега из высокомодульного или сверхвысокомодульного углеродного волокна обеспечивает существенно более высокое отношение жесткости к весу. Для очень требовательных приложений, где требуется максимальная жесткость, можно использовать сверхвысокомодульное углеродное волокно 110 msi. Это специальное углеродное волокно на основе смолы имеет жесткость на изгиб более чем в 3 раза больше, чем у стандартной препрег-панели с модулем упругости (около 25 msi). Когда кто-то рассматривает возможность индивидуальной жесткости панели из углеродного волокна за счет стратегического размещения ламината, панель (или другое поперечное сечение, такое как труба) может быть изготовлена с жесткостью на изгиб порядка 50 msi.
Все ориентированные под нулевым градусом однонаправленные сверхвысокомодульные образцы-купоны имеют жесткость при растяжении более 70 msi, что более чем в два раза превышает жесткость стали, но при этом вдвое легче алюминия. Отношение жесткости к весу этого материала более чем в 10 раз больше, чем у стали или алюминия. Если учесть потенциально значительное увеличение отношения прочности к весу и жесткости к весу, возможное, когда эти материалы сочетаются с легкими сотовыми пенопластовыми сердечниками, влияние передовых композитов из углеродного волокна становится очевидным.
Что такое сэндвич-структура из композитного углеродного волокна?
Композитный сэндвич сочетает в себе превосходные свойства прочности и жесткости углеродного волокна с материалом сердцевины более низкой плотности. В сэндвич-листах Dragonplate тонкая оболочка из углеродного волокна ламинируется поверх пенопласта, сотового заполнителя, бальзы или сердцевины из березовой фанеры. Комбинируя эти материалы, можно создать конечный продукт с гораздо более высоким отношением жесткости к весу. Для приложений, где вес имеет решающее значение, сэндвич-листы из углеродного волокна могут подойти.
Композитная многослойная конструкция Напряжения и напряжения в двутавровой балке
Композитная многослойная конструкция похожа на однородную двутавровую балку при изгибе.
Рис. 1: Схема, показывающая сэндвич из композитного углеродного волокна и эквивалентную двутавровую балку. равен нулю.
Двигаясь снизу вверх на диаграмме, внутренние напряжения меняются от сжимающих к растягивающим. Жесткость на изгиб пропорциональна моменту инерции поперечного сечения, а также модулю упругости материала.
Таким образом, для максимальной жесткости на изгиб необходимо поместить очень жесткий материал как можно дальше от нейтральной оси. Разместив углеродное волокно дальше от нейтральной оси и заполнив оставшийся объем материалом с более низкой плотностью, в результате получается многослойный композитный материал с очень высоким отношением жесткости к весу.
Рис. 2: Сравнение распределения внутренних напряжений для твердого ламината и многослойной конструкции при изгибе.
Анализ ламината с сердцевиной из березовой фанеры по сравнению с укладкой из цельного каронового волокна
Анализы FEA, сравнивающие уровни напряжения в многослойном многослойном материале и твердом углеродном волокне, показаны ниже. Эти расчеты показывают прогиб консольной балки с грузом на конце. На рисунке 3/16-дюймовый ламинат из березовой фанеры показан рядом с монолитным углеродным волокном равного веса. Из-за меньшей толщины цельного углеродного луча он прогибается значительно больше, чем эквивалентный стержень, изготовленный из материала сердечника. По мере увеличения толщины это несоответствие становится еще больше из-за значительной экономии веса за счет сердечника.Также можно заменить прочную углеродную конструкцию более легкой эквивалентной прочности и жесткости, изготовленной из любого из ранее упомянутых вариантов сердечника.
Рисунок 3: Сравнение методом конечных элементов многослойного многослойного материала Dragonplate и цельного углеродного волокна
Сильные и слабые стороны различных сердцевин из сэндвич-панелей из углеродного волокна
При использовании различных сердцевин каждый из них имеет сильные и слабые стороны. Как правило, движущими факторами являются прочность ядра на сжатие и сдвиг. Например, если требуется высокая прочность на сжатие (и, следовательно, высокая устойчивость к раздавливанию), то сердцевина, скорее всего, должна быть более плотной (здесь хорошим вариантом будет пенопласт высокой плотности или березовая фанера). Если, однако, требуется композит с максимально низким весом, а напряжения относительно малы (т. е. применение с низкой нагрузкой и высокой жесткостью), то лучшим выбором может быть чрезвычайно легкий пенопласт или сотовый заполнитель.
Некоторые наполнители обладают лучшей влагостойкостью (пенопласт с закрытыми порами), другие лучше поддаются механической обработке (фанера), а третьи имеют высокое отношение прочности на сжатие к весу (бальза). Инженер должен понять компромиссы в процессе проектирования, чтобы максимально использовать потенциал композитов с наполнителем.
Тем не менее, для критичных по весу применений часто нет другого варианта, который хотя бы приблизился к потенциальной прочности и соотношению жесткости к весу многослойных ламинатов с сердцевиной из углеродного волокна.
КРИТЕРИИ СРАВНЕНИЯ | |||||
ПРОДУКТЫ | Жесткость к весу | Прочность | Прочность | Влагостойкость | Звукопоглощение |
Твердое углеродное волокно | ХОРОШО | ЛУЧШЕ | ЛУЧШЕЕ | ЛУЧШЕЕ | ПЛОХОЕ |
Высокомодульное цельное углеродное волокно | ЛУЧШЕ | ХОРОШЕЕ | ЛУЧШЕЕ | ЛУЧШЕЕ | ПЛОХОЕ |
Березовое ядро | ЛУЧШЕЕ | ЛУЧШЕЕ | ЛУЧШИЙ | ХОРОШИЙ | ПЛОХОЙ |
Бальзовый сердечник | ЛУЧШИЙ | ХОРОШИЙ | ЛУЧШИЙ | ПЛОХОЕ | ХОРОШЕЕ |
Сотовый заполнитель из номекса | ЛУЧШИЙ | ХОРОШИЙ | ЛУЧШИЙ | ЛУЧШИЙ | ЛУЧШИЙ |
Пенный наполнитель Depron | ЛУЧШЕ | ПЛОХОЙ | ПЛОХОЙ | ЛУЧШИЙ | ЛУЧШИЙ |
Airex Foam Core | 903 03 ЛУЧШИЙХОРОШИЙ | ХОРОШИЙ | ЛУЧШИЙ | ЛУЧШИЙ | |
Вспененный наполнитель Divinycell | ЛУЧШЕ | ЛУЧШЕ | ЛУЧШЕ | ЛУЧШЕ | ХОРОШЕЕ |
Last-A-Foam Core | ЛУЧШЕ | ЛУЧШЕ | ЛУЧШЕ | ЛУЧШЕ | ЛУЧШЕ |
Плюсы и минусы композитов из углеродного волокна многослойные волокнистые сэндвич-ламинаты, углеродные трубки и т.
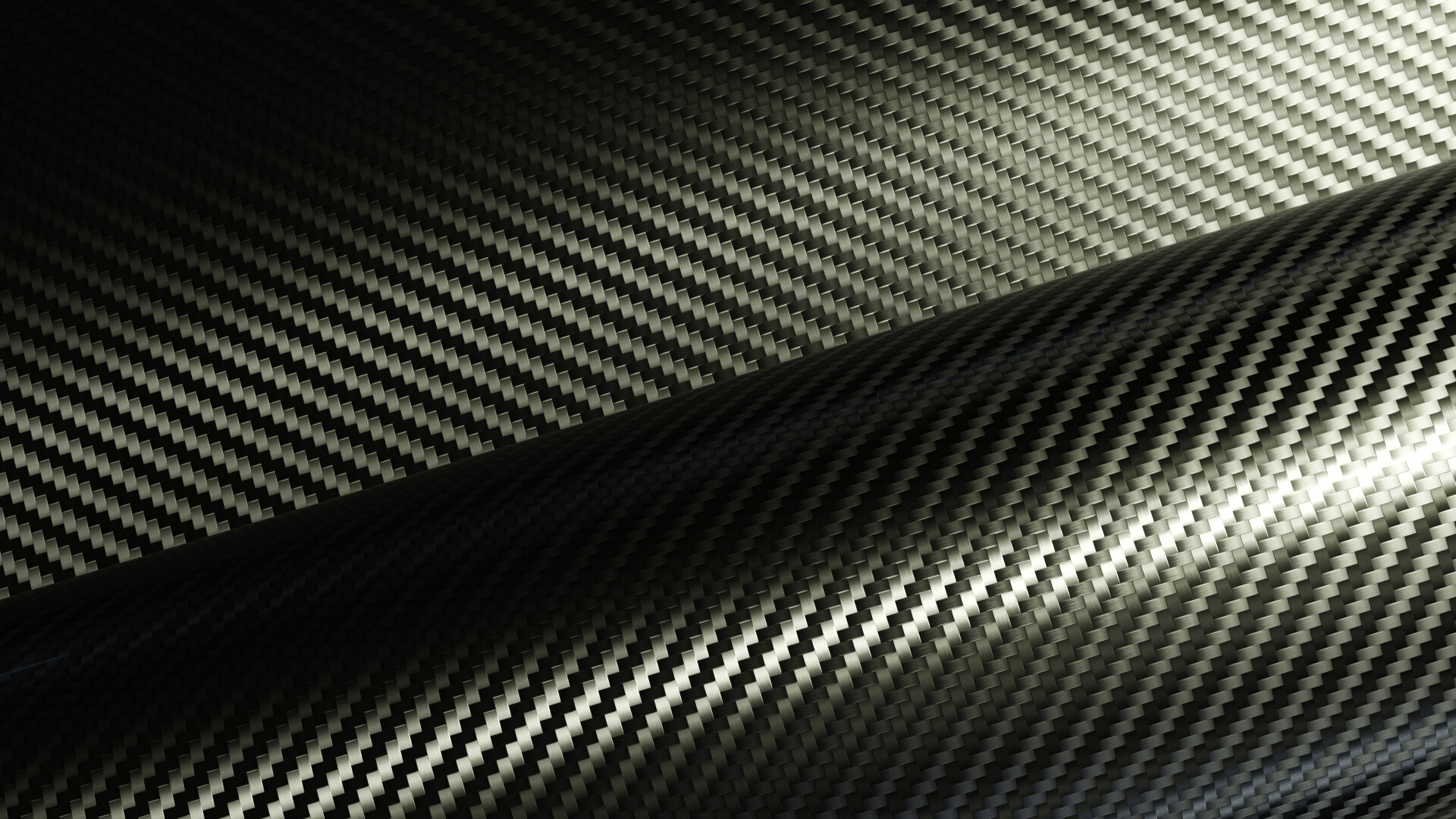
Плюсы:
- Отношение прочности к весу
- Отношение жесткости к весу
- Электропроводность
- Теплопроводность
- Углеродное волокно пластически не уступает 9002 2
- Уникальная и красивая поверхность
Высокая Прочность может быть достигнута в сочетании с другими материалами. В некоторых приложениях также используется электропроводность углеродного волокна, а также высокая теплопроводность в случае специализированного углеродного волокна.
Минусы:
- Как только предел прочности будет превышен, углеродное волокно внезапно и катастрофически выйдет из строя.
- Материалы из углеродного волокна значительно дороже, чем традиционные материалы
- Работа с углеродным волокном требует высокого уровня квалификации и специального инструмента для производства высококачественных конструкционных материалов
- Углеродное волокно не поддается. Под нагрузкой углеродное волокно изгибается, но не остается постоянно деформированным. Как только предел прочности материала будет превышен, углеродное волокно внезапно и катастрофически выйдет из строя. В процессе проектирования очень важно, чтобы инженер понимал и учитывал такое поведение, особенно с точки зрения расчетных коэффициентов безопасности.
Углеродное волокно и металлы
При проектировании композитных деталей нельзя просто сравнивать свойства углеродного волокна со сталью, алюминием или пластиком, поскольку эти материалы в целом однородны (свойства одинаковы во всех точках детали). ) и имеют изотропные свойства на всем протяжении (свойства одинаковы по всем осям). Для сравнения, в детали из углеродного волокна прочность находится вдоль оси волокон, и, таким образом, свойства и ориентация волокон сильно влияют на механические свойства. Детали из углеродного волокна в целом не являются ни однородными, ни изотропными.
Изготовление из углеродного волокна для пользовательских применений
Свойства детали из углеродного волокна близки к свойствам стали, а вес близок к пластику. Таким образом, отношение прочности к весу (а также отношение жесткости к весу) детали из углеродного волокна намного выше, чем у стали или пластика. Конкретные детали зависят от конструкции детали и применения. Например, пенопластовый сэндвич имеет чрезвычайно высокое отношение прочности к весу при изгибе, но не обязательно при сжатии или раздавливании. Кроме того, нагрузка и граничные условия любых компонентов уникальны для конструкции, в которой они находятся. Таким образом, мы не можем предоставить толщину пластины из углеродного волокна, которая заменит стальную пластину в вашем приложении.